GE Plans World's Largest Laser-Powered 3D Printer The Atlas printer is designed to churn out parts up to one meter long, including entire engine blocks for automobiles.
By Tom Brant
This story originally appeared on PCMag
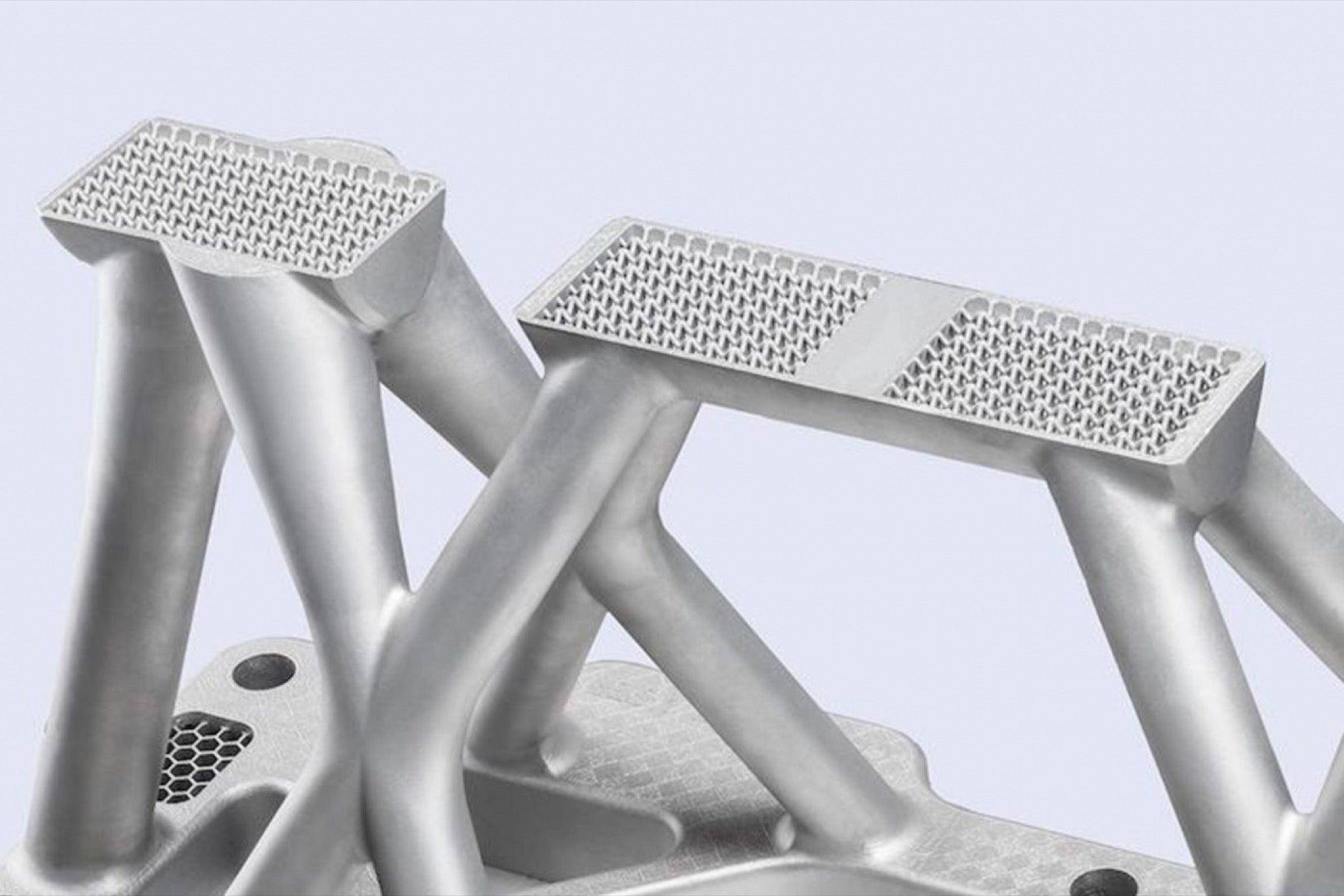
General Electric is poised to start churning out the world's largest laser-powered 3D printer that makes parts out of metal powder, delivering examples to factories next year so that they can get started making airplane parts and products for the automotive, power and oil and gas industries.
The prototype Atlas printer, announced on Wednesday, can print objects up to one meter long using titanium, aluminum and other metals instead of the plastics, resins, and filaments that many commercial and consumer 3D printers use. That means it could print an entire engine block for a car or truck, for example, replacing the specialized machines and tooling that are currently required to make those types of products in a factory.
GE said it plans to unveil the Atlas in November. The prototype can only print objects up to one meter in two directions, such as length and width, but once the production version is ready next year, it will be able to print objects up to one meter in any direction.
While GE is busy working on its laser-powered Atlas behemoth, Volkswagen is already seeing the benefits of a more conventional approach to 3D printing. The automaker announced this week that engineers and line technicians are using off-the-shelf Ultimaker 3 and Ultimaker 2+ printers at the Volkswagen Autoeuropa factory in Portugal, which makes 100,000 cars per year. Instead of printing parts for the cars themselves, the printers churn out custom-designed tools like gauges, jigs and fixtures for the factory's 4,000 workers.
Volkswagen said that the 3D printers now make 93 percent of the tools that Autoeuropa factory used to buy from external vendors, saving $150,000 last year.
"In addition to the time and cost savings we realize, the tools we output are more complex and ergonomic -- and, ultimately, far more useful in our day-to-day operations because they are tailored to our needs," Luis Pascoa of Volkswagen Autoeuropa said in a statement.