Why Executives Need to Take Note of 'Digital Twins' It is a concept, not a single product or a piece of technology
Opinions expressed by Entrepreneur contributors are their own.
You're reading Entrepreneur Asia Pacific, an international franchise of Entrepreneur Media.
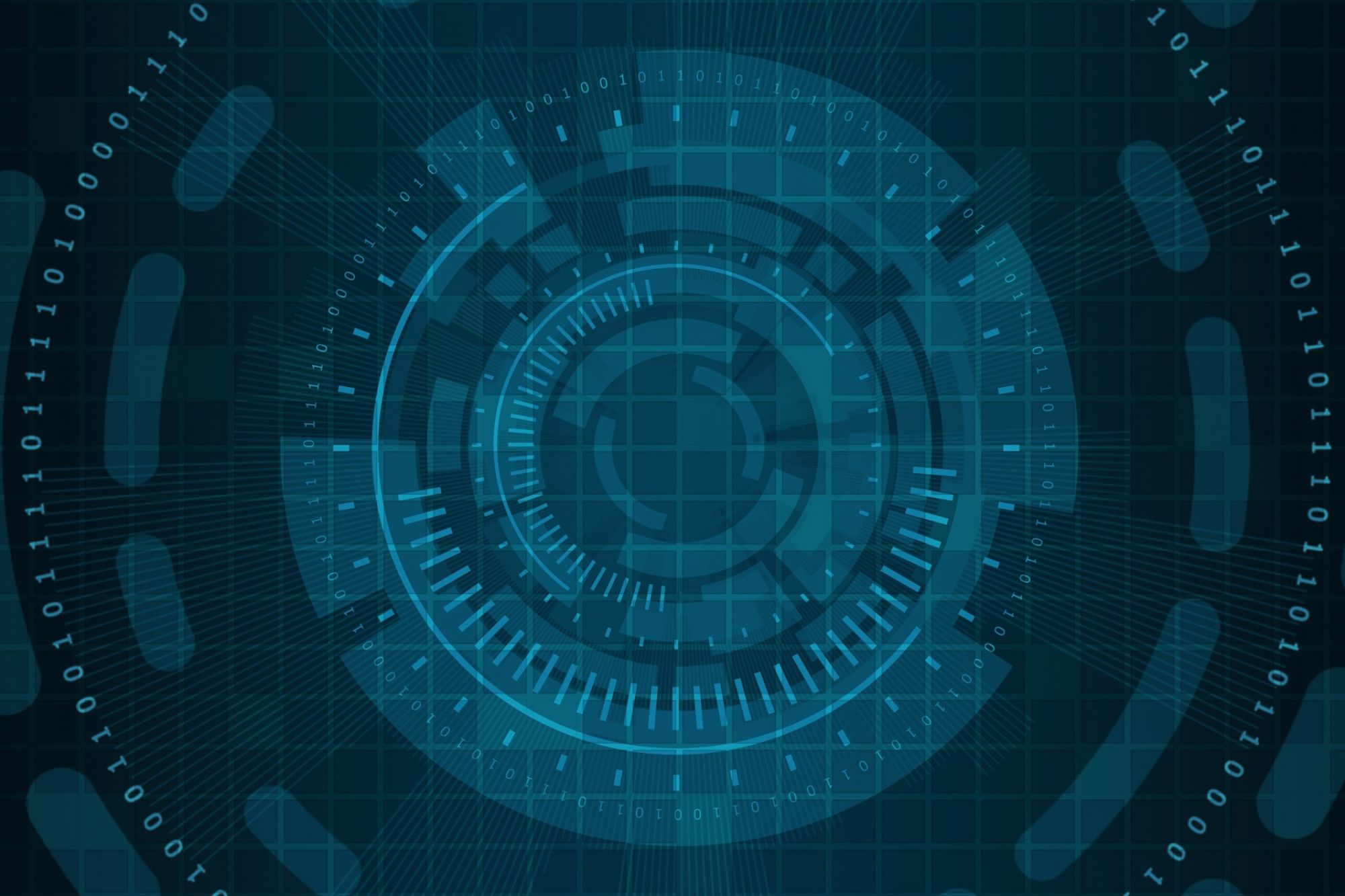
"Digital Twins", as a concept, has been around for a while. Michael Grieves at the University of Michigan in the US wrote about it in a whitepaper in 2002. NASA's been long using Digital Twins for its space mission, as they (obviously)don't have physical access to the equipment, once it leaves our planet. Simulation and visualization technologies have been in use for decades. Yet, Digital Twins didn't capture the imagination of enterprises, until recently.
The proliferation of IOT devices, the ability to gather and manage big data, and the emergence of sophisticated analysis and prediction technologies, are now pushing the adoption of Digital Twins. Gartner named Digital Twins as the Top 10 Strategic Technology for 2017, fueling the imagination of enterprises. From there, it's been a growth story.
What are Digital Twins? Why are they important? Why should the executives take note of them? Let's explore.
Demystifying Them
Firstly, Digital Twins is a concept, not a single product or a piece of technology. Multiple technologies, 3D simulation, IOT, 4G/5G, big data, blockchain, Edge and cloud computing, and artificial intelligence come together to make the concept a reality.
The core principle is, for a physical entity or an asset, a digital equivalent exists in the virtual world. With the world around us being fitted with sensors, it is now possible to replicate the physical properties and characteristics in the digital form. Practically any physical entity or an asset ̶a car, an airplane, an entire factory and even human beings ̶ can have sensors transmitting information on a real-time basis to its digital twin. In turn, the digital twin, feeds the physical twin with opportunities for optimization.
The real-time two-way communication and synchronization between the physical twin and the digital twin, enables a variety of prognostics and diagnostics opportunities for the enterprises.
Its Benefits
Digital Twins are meant to strengthen the design-execute-change-decommission lifecycle. Naturally, from conceptualizing to decommissioning, digital twins find a place in the product lifecycle. Broadly, there are three types of digital twins – Product Twin, Production Twin and Performance Twin (terms made popular by Siemens):
- Product Twins: Designing a physical asset is a complex and expensive phase of the product lifecycle. Though the world of design has evolved from 2D-blueprints to standalone 3D-simulations, R&D is still constrained by limited collaboration. Testing prototypes demands a high-level of human expertise to prevent losses due to errors. Furthermore, undesired/unexpected behavior in the real-world means going back to the drawing board and making expensive changes to the design.
The concept of twins is no stranger to the software R&D – multiple environments can be spun off easily and inexpensively to simulate scenarios. Digital Twins will bring the same level of flexibility to the hardware/physical R&D. With Digital Twins, organizations can design models collaboratively with the user groups and simulate various test conditions. Without the fear of cost overruns and need for experienced professionals, prototypes can be put under both constructive and destructive testing. Not only do the R&D costs come down with a virtual sandbox environment, the quality of the end-product has also been observed to improve.
- Production Twins: Smooth running of operations are critical for any business. Despite digital transformation, many operations and production process are still in silos and doesn't provide a complete picture of the production orchestra. In many moving parts ̶which is often the case with physical entities ̶ critical information like clashes and conflict among the parts, are not captured in the digital world. When dozens of variables impact a production process, it's humanly impossible to simulate and control all situations.
Digital Twins, in addition to providing insights into parts and components, have the potential to enable visibility into the large interconnection of the production environment – an entire process, factory or even a city. By enabling models of virtual production units, Digital Twins leverage real-time data and technology to optimize the production process, for the people running the unit. Humans now can ask what-if questions and simulate their impact, without destabilizing the production environment. Any changes to an in-use state, gets reflected in the Digital Twin – a chronic operational problem resolved for systems that undergo frequent part and configuration changes.
- Performance Twins: An unnecessary downtime, failure or damage is every enterprise's nightmare. Any aspect of the 5M – Man, Machine, Material, Method and Management – can lead to an undesired result. End result? Many operations struggle fire-fighting with poor knowledge management. Even timely knowledge of what-has-happened becomes an uphill task, in the absence of detailed root-cause-analysis procedures.
In Digital Twins, the physical properties and data from the sensors and operating environment are being combined with sophisticated prediction algorithms. Digital Twins can help enterprises move to a state of predicting "what is likely to happen" from "what has happened". Digital Twins also serve as a knowledge management framework, storing historical state and performance, predicted future state and design-information. With Digital Twins, enterprises are aspiring for strong interrogative (past) and superlative prediction (future) capabilities.
Industry Outlook
Given the benefits, CIOs are looking to Digital Twins as the key framework for monetizing their IOT investments (Forrester research).For the past couple of years, Digital Twins are consistently featuring in prominent industry analyst and researchers reports. Various market research data has projected the Digital Twin segment growth at 38 per cent CAGR, to reach US$ 32.36 billion by the year 2025.
Naturally, industries with higher IOT penetration like aerospace, defense and automotive are at the forefront for deploying Digital Twins. Realizing the potential, other segments like manufacturing, energy and utilities, infrastructure, telecommunications, healthcare and even agriculture, are building Digital Twin use cases for their Industry 4.0 initiatives.
Digital Twin cities are being used to simulate disaster response and planning, surgeons are operating on a digital heart before making an incision on the skin, and infrastructure grids are using Digital Ghosts (a spin-off of Digital Twins) for identifying and fixing vulnerabilities. Interesting times ahead, as the real and the virtual worlds merge.