Daimler Trucks To Use 3D Printing in Spare Parts Production Daimler, the world's largest truck manufacturer, will use three-dimensional printing to produce spare parts, the latest example of how digital technologies are radically reshaping automotive manufacturing and its supply chain.
By Reuters
This story originally appeared on Reuters
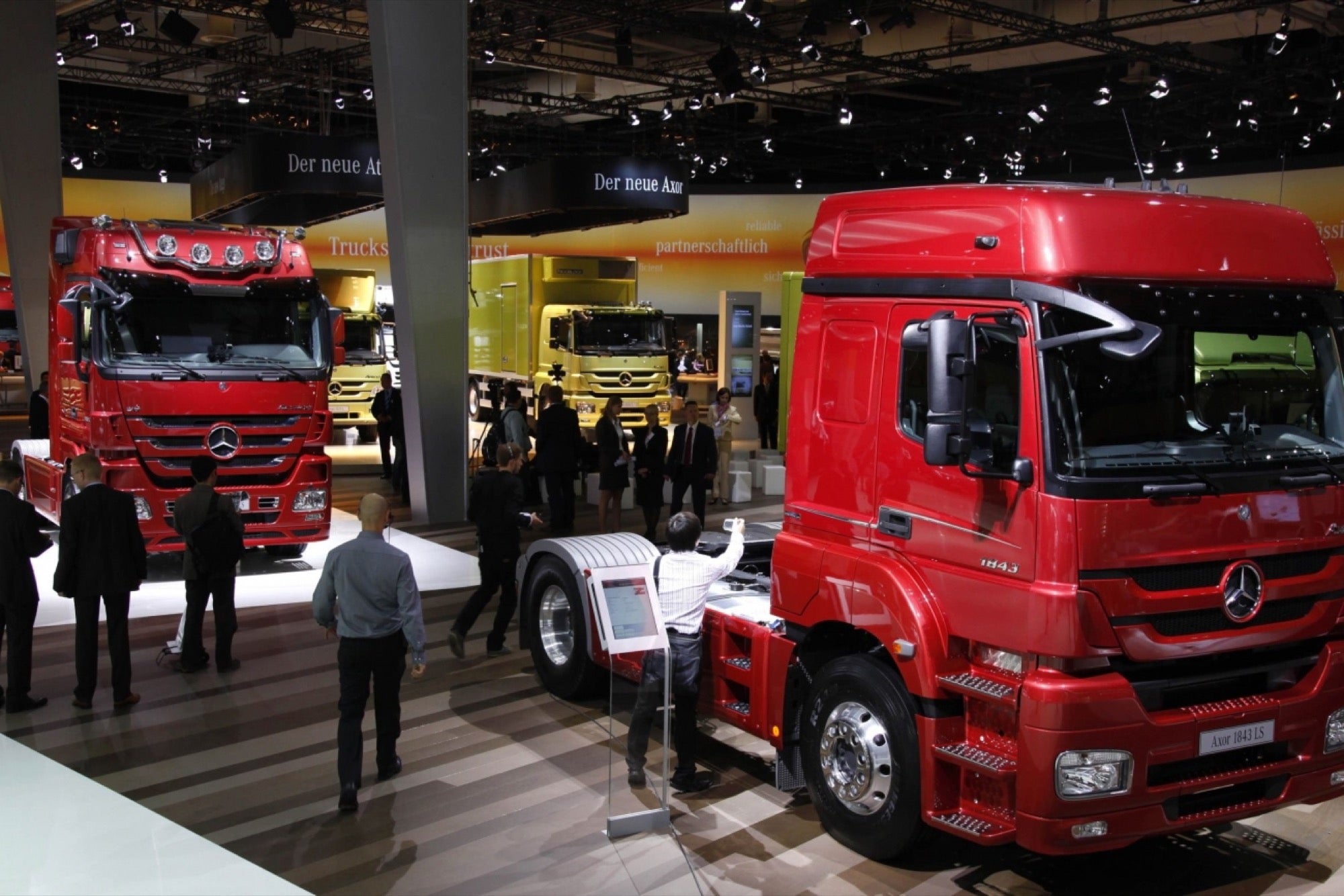
Daimler, the world's largest truck manufacturer, will use three-dimensional printing (3D) to produce spare parts, the latest example of how digital technologies are radically reshaping automotive manufacturing and its supply chain.
Rather than shipping vehicle parts across the globe, carmakers including BMW and Volkswagen are experimenting with so-called additive manufacturing. This relies on sending a digital blueprint of a component to a printer which creates parts by using lasers to melt powders into plastic, glass, metals and even ceramics.
By printing new parts, automakers can save logistics and warehouse storage costs and produce complex components at low volumes.
The technology is not ready to make high-volume vehicle components, so carmakers rely on conventional manufacturing methods for components like metal body panels, which are made using hydraulic metal stamping presses, costing up to 40 million euros ($44 mln) each.
But advances in laser technology, thermal and chemical processes mean 3D printing can be used for some small batches of customized components, for things like prototype vehicles and concept cars.
In a sign of the technology becoming more widespread, Daimler Trucks said on Wednesday that from September, it will use 3D printing processes for plastic spare parts including spring caps, air and cable ducts, clamps, mountings and control elements.
Daimler, which owns the Mercedes-Benz brand, has more than 100,000 printed prototype parts, and said it will expand production using 3D printing methods.
The truck maker's "printed" spare parts are created with 3D printers based on what is known as a selective laser sintering (SLS) printing process, and ordered using a special spare part number, even for parts on models that are several decades old or even out of production.
Rival Audi said on Wednesday that it is creating a 3D competence center at its factory in Ingolstadt, Germany, year end, to develop production of components made from steel and aluminium. From October onward, Audi will use printers to make steel tools.
Volkswagen and BMW have used 3D printing for years in the process of "rapid prototyping."
The cost of additive manufacturing is expected to fall by between 25 percent and 45 percent until 2020, thanks to multi-laser machines and improvements in the powder-dispensing process, management consultants Roland Berger said.
Compared to the conventional machine tool market, the metal "additive manufacturing" market has less than 1 percent market share, according to Roland Berger.
Three-dimensional printing has been used by the aircraft industry. The United States Navy has installed systems on combat ships to produce spare parts, for example to repair the nose cone of a damaged Harrier jet.
BMW has experimented with 3D technology since the 1990s, using 3D printing to make components for the Rolls-Royce Phantom, including the casing of the indicator light.
BMW sees major potential for the future application for new customer offerings, such as personalized vehicle parts, it has said.
(Additional reporting by Irene Preisinger; editing by Louise Heavens and Susan Fenton)