Go Green Or Go Home: 3 Ways Industrial Facilities Can Clean Up Their Acts Out with toxic emissions, in with environmental sustainability.
By Farhana Rahman Edited by Dan Bova
Opinions expressed by Entrepreneur contributors are their own.
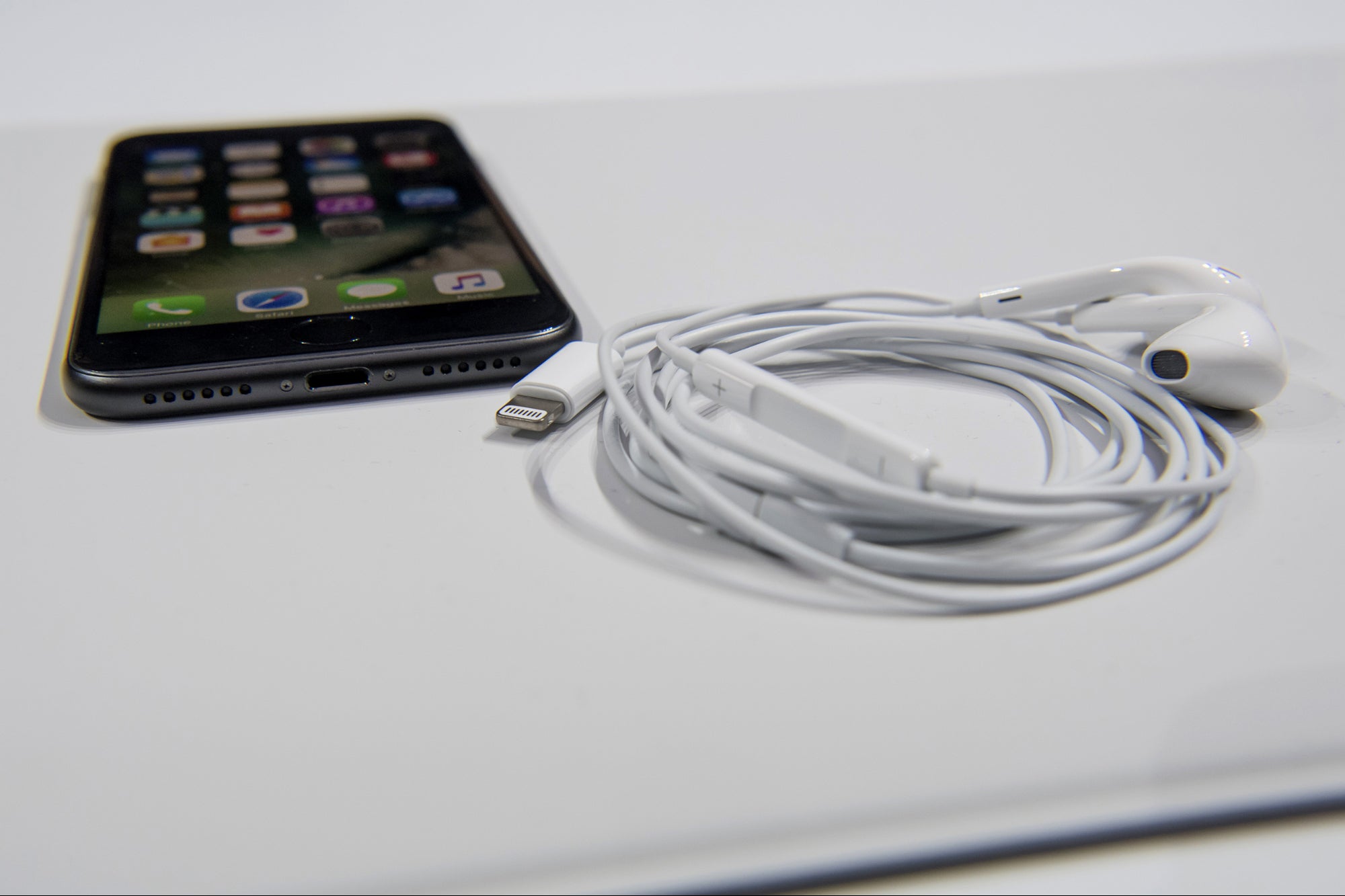
Industrial facilities, such as manufacturing plants and factories, have long garnered a reputation for not being environmentally-friendly. The negative impact is visible when driving by such facilities, through the odorous smokestack emissions that cause harm to the atmosphere. However, there are also facilities that contribute to land and water pollution by acidifying rain, chemical spills and disposal of toxic waste. Their damage often goes unseen.
In response to the ever-rising public demand for environmental sustainability, coupled with higher taxes on emissions, factories did indeed start making necessary changes in recent years, and they have made a huge difference. According to a report by the United States Environmental Protection Agency:
"From 1995-2019, annual emissions of sulfur dioxide from power plants fell by 92 percent and annual emissions of nitrogen oxides from power plants fell by 85 percent. In 2019, sources in both the Cross-State Air Pollution Rule (CSAPR) sulfur dioxide annual program and the Acid Rain Program together emitted 0.97 million tons, a reduction of 10.8 million tons, or 92 percent, from 1995 levels. In 2019, sources in both the CSAPR nitrogen oxides annual program and the Acid Rain Program together emitted 0.88 million tons, a reduction of 5 million tons, or 85 percent, from 1995 levels."
Related: Easy Ways to Make Your Business More Sustainable
While those numbers are promising, there is still much that factories must do in order to go green on a global scale, considering the world is on the cusp of irreversible environmental damage that was caused by humankind.
Here are some of the most impactful ways that industrial facilities can make the switch to go green.
Switch from nuclear energy, to clean energy sources
The usage of coal or natural gas to generate electricity is one of the largest contributors to water and air pollution worldwide. In turn, the pollution is often linked to chronic health concerns, such as heart attacks, neurological damage, breathing problems, and cancer. On the flip side, clean energy that is generated from solar power and/or wind contributes no air pollution whatsoever.
In cases where making the switch to clean energy is genuinely not an option, biomass and geothermal systems count as decent middle ground. While they do create some air pollutants, it's at a significantly lower level in comparison to coal-fired plants or natural gas.
Also, when using systems that create air pollutants, there are ways to destroy those elements before they enter the earth's atmosphere. Alternative Energy Magazine highlights the following three mechanisms that have been created to do just that:
Catalytic oxidizers: These machines use intense temperatures and chemical catalysts to render air pollutants down into their constituent compounds, which may then be harmlessly released.
Regenerative thermal oxidizers (RTOs): With RTOs, factories repurpose industrial waste heat to destroy pollutants within networks of heat exchangers.
Rotary concentrators: Like the name suggests, rotary concentrators rotate at high speed to separate air pollution into a hydrophobic media, where an oxidizer destroys it.
Turn to win-win processes and solutions to help the business and the environment
It is recommended for industrial facilities to explore ways to keep unnecessary products out of the supply chain and distribution networks because it ultimately becomes a clear win-win for all. Doing so will cut costs, keep the focus on core products, and reduce the amount of solid waste in landfills, which happens to be one of the largest contributors of methane gas emissions. Apple made headlines by making this move when it decided to ship the iPhone 12 without a charger or earpods. According to an official statement by Lisa Jackson, the vice president of environment, policy, and social initiatives at Apple, "There are also over 2 billion Apple power adapters out there in the world, and that's not counting the billions of third-party adapters. We're removing these items from the iPhone box, which reduces carbon emissions and avoids the mining and use of precious materials."
Related: How to Create a More Sustainable Supply Chain
A simple upgrade in processes and technologies can also serve as a win-win for industrial facilities. In addition to significantly reducing energy waste, it can also optimize efforts in maintenance. This is seen with companies such as Ecoplant, which provides a SaaS solution that connects to the controllers of air compressors and property sensors to monitor and optimize systems. Such a solution can easily cater to industrial plants from all sectors (including food, steel, and plastic) to enable continuous savings for the facilities themselves, while simultaneously catering to environmental laws, regulations, and standards.
Most people don't know how integral air compression is to almost all industrial production. According to the U.S. Department of Energy, 90% of factories use air compression, and it accounts for up to 30% of the average factories' energy consumption. Half of the energy for air compression is wasted due to leaks and other inefficiencies. With numbers like these, it's easy to understand how this costs companies hundreds of thousands of dollars, and wastes energy at a scale the world cannot afford.
Use materials that do not have the potential to become toxic
Technically speaking, raw materials are not always toxic. But they do have the potential to become toxic after undergoing processes such as milling and grinding. In a report on contaminants and remedial options, the United States Environmental Protection Agency recommends that manufacturers replace raw materials and additives containing chromium, mercury, and lead with non-hazardous biocide alternatives. This replacement will help maintain desirable bacteria-eliminating properties, without running the risks to health and air quality that are posed by toxic-heavy metals.
Related: 3 Trends Shaping the Future of the Consumer Goods Industry
In cases where there simply aren't any convenient material substitutions that can be made, proper training and protective equipment must be supplied to workers that will handle the potentially hazardous materials.
If they haven't already in their own unique way, industrial facilities must go green or go home. According to McKinsey & Company, using the right technology in manufacturing will lower costs in the range of $200 to $600 billion across the manufacturing industry. Going green saves manufacturers operational costs and tax money while helping them cater to demands for environmental sustainability, as well as legal needs, rules, and regulations.