How Covid-19 Served As an Inflection Point For Industrial Tech While pandemic speeded the adoption of industrial tech, there are still a wide range of problems in existing manufacturing processes that deeptech could solve
By S Shanthi
Opinions expressed by Entrepreneur contributors are their own.
You're reading Entrepreneur India, an international franchise of Entrepreneur Media.
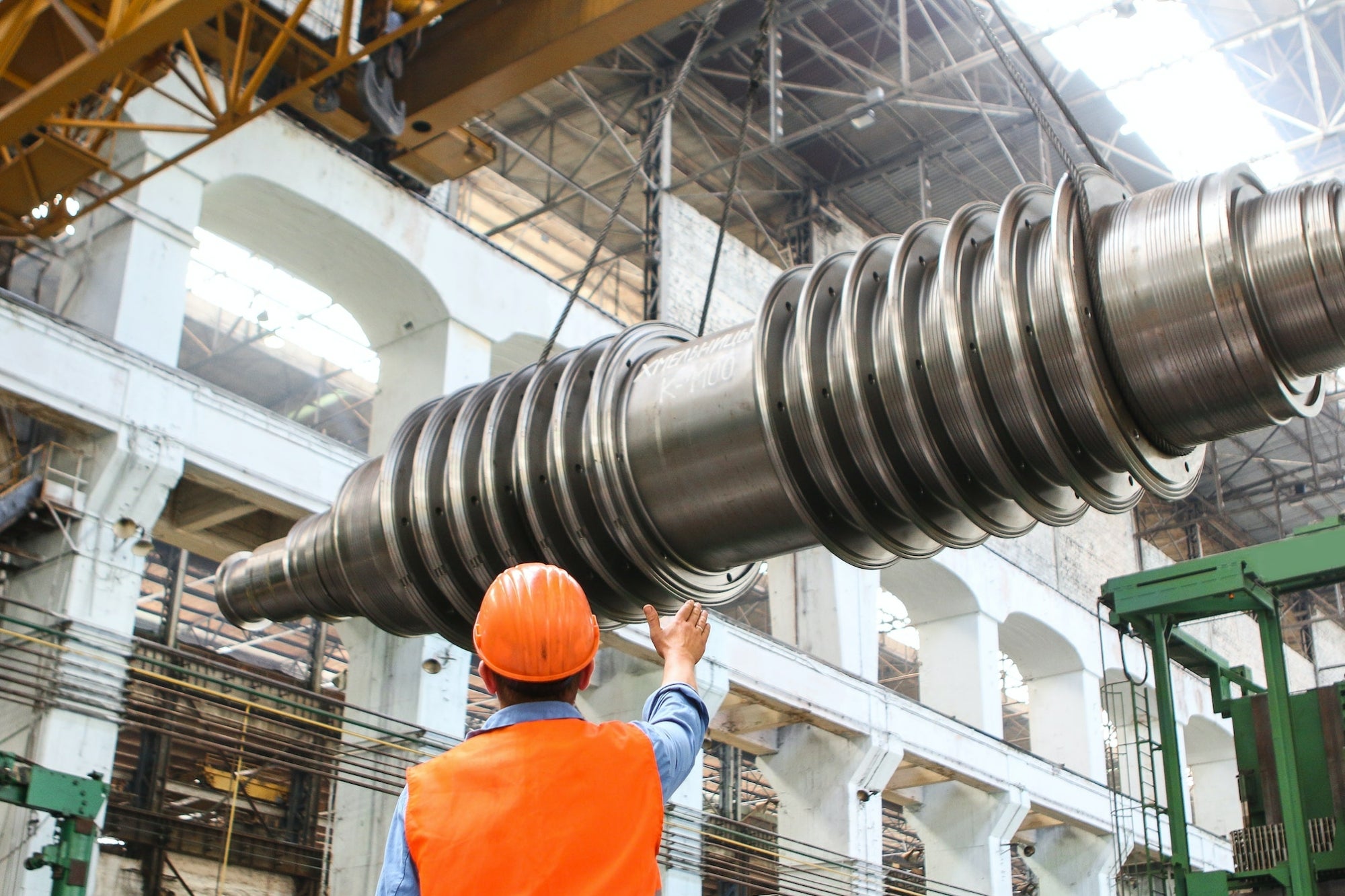
The pandemic has brought in a paradigm shift in the manufacturing industry in terms of digital adoption. According to IBEF data, the manufacturing sector of India has the potential to reach $1 trillion by 2025.
The pandemic has made Industry 4.0 a reality. A McKinsey analysis suggests three outcomes of the pandemic: a win for companies that had already scaled digital technologies, a reality check for those that were still scaling, and a wake-up call for those that hadn't started on their Industry 4.0 journeys.
The pandemic altered the industry's outlook in several ways. For instance, it demonstrated that technology can enable remote operations and create new business opportunities. "The pandemic also highlighted the critical role of resilience in the industrial sector. Businesses have had to adjust to shifting market conditions and supply chain disruptions, prompting a greater focus on supply chain resilience and contingency planning. This has led to investments in technologies that can improve supply chain visibility, reduce reliance on single suppliers, and facilitate more agile manufacturing processes," said Rajesh Khosla, CEO and president of AGI Glaspac.
Driven by deeptech startups, which came up with industry-specific solutions, Indian manufacturers have been increasingly investing in emerging technologies with a greater focus on competitiveness. "In addition to automation, startups have also been instrumental in developing other industrial tech solutions, such as remote monitoring and predictive maintenance, which have helped companies minimize downtime and improve operational efficiency, even with limited on-site staff," said MSR, CEO, T-Hub.
Gaps that deeptech can fill further
While pandemic speeded the adoption of industrial tech, there are still a wide range of problems in existing manufacturing processes that deeptech could solve, including quality control, predictive maintenance, process optimization, supply chain management and worker safety. By leveraging advanced technologies such as AI, machine learning and IoT, manufacturers can improve efficiency, reduce waste and improve the overall safety and quality of their products.
"The deeptech ecosystem in India has been making significant progress in the global innovation ecosystem. Startups are leveraging disruptive technologies, such as AI/ML, NLP and blockchain to solve many socioeconomic challenges and enabling the country to achieve its ambitious economic goals. With the support of the government and the startup ecosystem, India's deeptech startups are poised to drive innovation and make a positive impact on society," said MSR.
Deeptech has been transforming the global manufacturing landscape and early adopters are reaping the benefits of increased productivity, efficiencies and lower costs. Soon, deeptech is expected to play an even bigger role in India too to realize its $1 trillion potential, experts say.
"The next major wave for industrial tech should entail efficiencies and innovation driven by leveraging deeptech like artificial intelligence (AI), machine learning (ML), IoT, blockchain, big data and analytics, augmented reality (AR), virtual reality (VR), robotics, 3D printing, drones, etc. These have the potential to redefine or create new markets," said Madhukar Bhardwaj, VP, BD & Investments, Inflection Point Ventures.
He further added that in this decade, we should expect an amalgamation of digital insights (sensors and embedded software in products), digital continuity (creating and managing virtual models) and digital convergence (digitalization of core processes in an extended ecosystem of enterprise IT systems).
Experts believe that we are yet to fully reap the benefits of deeptech in manufacturing and to do that investment in upskilling the workforce is necessary. Additionally, infrastructure improvements, such as high-speed internet connectivity and reliable power supply, are crucial to support the implementation of these solutions. Khosla also suggests that regulations must be in place to ensure the safe and secure use of these technologies while fostering innovation and growth.
"Many companies are still using traditional manufacturing methods and have yet to embrace the potential of Industry 4.0 fully. Additionally, there are challenges related to the cost of implementing these technologies and the need for skilled professionals to manage them. Another area where India's manufacturing sector could improve is the adoption of automation and robotics. While some companies have started to automate specific processes, there is still a significant amount of manual labour involved in the manufacturing process in India," said Siddhant Bery, managing partner and CEO, KSP Inc.
Advanced technologies that are yet to be adopted
While the Indian manufacturing sector has made significant progress in recent years, some advanced technologies are yet to be widely adopted. The slow adoption rate compared to developed economies can be attributed to various reasons, such as lack of infrastructure, access to finance and skilled workforce, among others. Here are some of them, as shared by MSR.
Cyber-physical Systems (CPS): CPS is an emerging technology that integrates physical and cyber systems to create a new generation of intelligent and interconnected products, machines and systems. The adoption of CPS can bring significant benefits to the manufacturing industry, such as increased efficiency, improved quality and reduced costs. However, the complexity of CPS and the lack of awareness and skilled workforce are the primary reasons for its slow adoption.
Augmented Reality and Virtual Reality (AR/VR): AR and VR technologies have tremendous potential in manufacturing industries, and their adoption can help in improving efficiency, reducing costs and increasing safety. However, the high cost of implementation, lack of infrastructure and lack of awareness are some of the reasons for their slow adoption.
Edge and cloud computing: Edge and cloud computing are critical technologies for the manufacturing industry as they help in processing and analyzing data in real-time, enabling quick decision-making and reducing downtime. However, the adoption of these technologies requires significant investment in infrastructure and skilled workforce, which is a challenge for small and medium-sized enterprises.
Cybersecurity: With the increasing convergence of IT and OT, cybersecurity has become a critical concern for the manufacturing industry. The lack of awareness and skilled workforce in cybersecurity, coupled with the high cost of implementing secure solutions, is the primary reason for the slow adoption.
Digital supply chain: It involves using digital tools, such as integrated warehousing and freight handling to strengthen procurement strategies for manufacturing units. Startups in the B2B commerce space, such as Moglix, are creating a promising future for the manufacturing sector by providing digital solutions of supply chain management.
Harnessing Big Data in Manufacturing: Manufacturing generates more data than any other sector of the economy, and companies can harness this data for decision-making by using MRP (material requirements planning) system, SAP, Oracle or ERP systems.
Blockchain technology: This technology, which is a distributed ledger where transactions conducted on the platform are visible to everyone, has been identified as a potential disruptor in the automotive industry. It has transformative potential across industries in manufacturing. It can also be used for smart contracts, payment systems and inventory management.