Four Things You May Not Know About Industry 4.0 It's not fiction, it's not the future, it's the reality of manufacturing today.
Opinions expressed by Entrepreneur contributors are their own.
You're reading Entrepreneur Middle East, an international franchise of Entrepreneur Media.
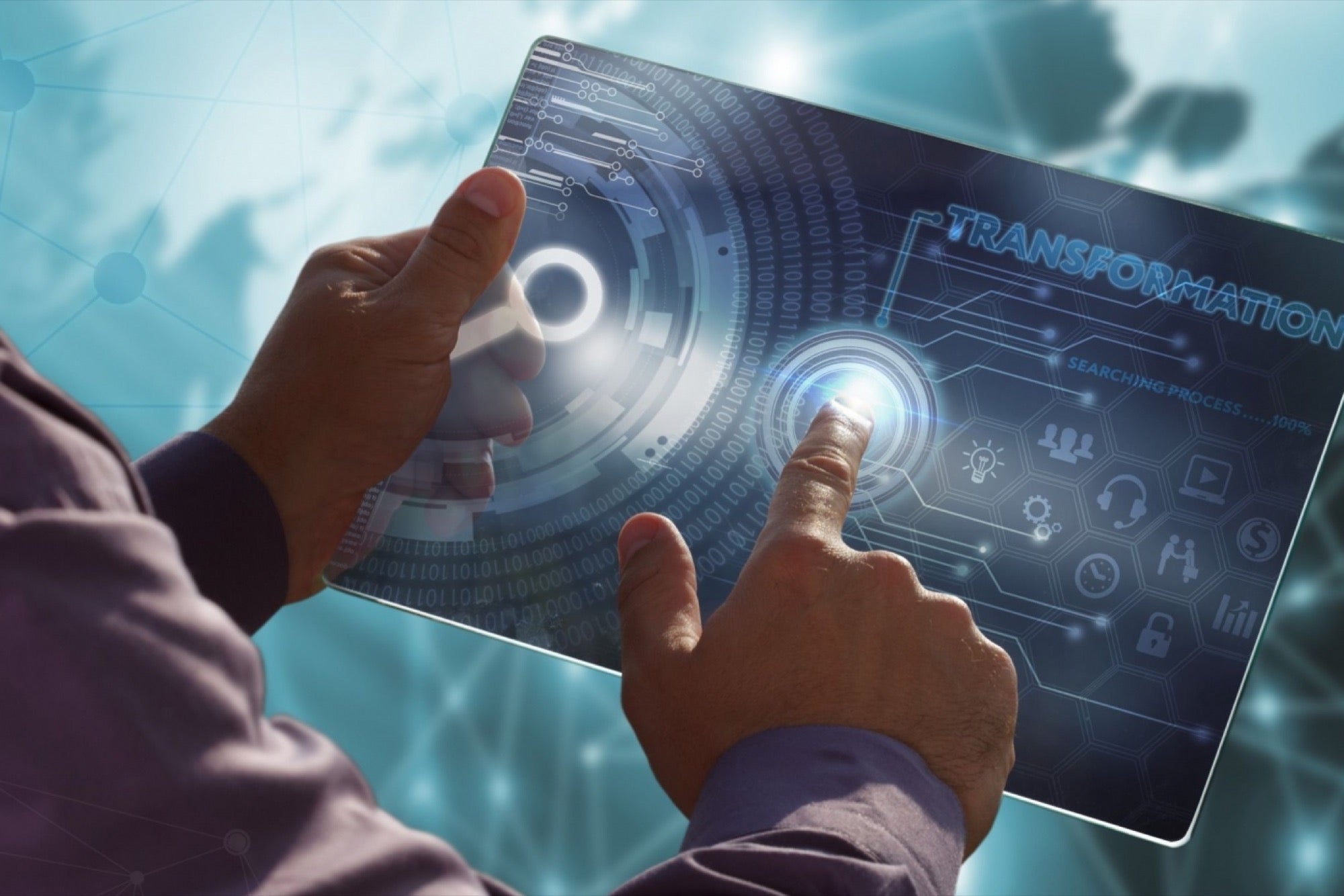
When we think about the first industrial revolution, we imagine heavyweight iron machinery. As we enter a new era in industrial manufacturing, we couldn't be further away from that. Smart, intelligent machines are improving our lives– both on an industrial scale and in our homes. It's been termed Industry 4.0 and has been gaining attention on the global stage. But what does it actually mean and what are its applications in everyday life? Here are four things you may not know about Industry 4.0:
1. Old machine + rapid connectivity = new benefit
Industrial scale machinery is a big investment– for manufacturers to make the most of their machinery today and optimize efficiency, connecting machinery to the internet is the next step. But in reality, many machines used in skilled trades or manufacturing are still not connected. Investing in all new machinery doesn't have to be the only solution – actually, lots of old machinery can be retrofit with solutions: the sensors, the software and connections– to bring them into the new industrial age. This enables things such as predictive maintenance, reducing downtime while increasing productivity– an investment that can pay for itself in just 18 months, versus buying new machinery.
2. Open standards = open economy
Bosch is helping to remove one of the biggest barriers for smaller companies seeking to enter the connected industry. The company is seizing the initiative and presenting a new, open industry standard it has developed in-house for the exchange of data in connected industry. This will enable interplay between a wide variety of partners in the internet of things (IoT) and in Industry 4.0. The new standard will, for instance, support the quick, easy, and secure transfer of data from sensors that SMEs supply to manufacturers to the production systems of large companies. The protocol is freely available and free of charge. Letting companies of all size exchange data will increase innovation and competitiveness, as well as help Industry 4.0 become more widely established. This is good news for the global economy, as well as here in the UAE, where there are strategic government visions in place to drive industrial and manufacturing development.
3. Automation = new job opportunities
There's been a lot of talk that with the rise in automation of services as seen in Industry 4.0, human capital will pay the price. And while it means that there may be a redistribution of workforce, it paves the way for new opportunities. Actually, Industry 4.0 opens the door to a whole new workforce in areas such as mechatronics engineering, industrial mechanics, and electrical engineering for automation technology. For the younger generation, now is the time to consider choosing STEM areas of study; the career possibilities are endless as Industry 4.0 expands across all sectors.
4. Connected technology = ease and efficiency for consumers
Imagine, you want to buy a new car– but in this age of personalization, you want to make it your own, and give it the personal touch. Once you've configured the car of your dreams, the personalized data is transmitted to the manufacturer's information systems. Your design data is connected and shared with different systems, flowing in two directions– to the manufacturing floor and to suppliers, to ensure parts and materials are ready for production. This forms a network between manufacturer and supplier. Once connected, a basic chassis and all the required materials are given an ID tag. This tag enables the parts to guide themselves through the factory– the products are in the right place, at the right time, for maximum efficiency.
When the chassis passes an intelligent station, its ID tag is scanned. Your design data is transferred to a cloud server and interactive communications platform, which runs all relevant production line data in real time; intelligently connecting man, machine and production. But this doesn't mean that factories will no longer need human talent; Industry 4.0 technology actively assists assembly workers. The technology is fine-tuned to workers' individual capabilities to boost their efficiencies. Even handheld tools have smart technology to connect man and machine better– making wrong assembly impossible. Now, you are eagerly awaiting your car– you don't want to experience a delay. Supposing one of the machines in the production line is about to breakdown? Since it is part of the Industry 4.0 platform, the data generated by the machine predicts the breakdown before it happens. This means no more pulling out repair manuals; workers can use video goggles and augmented reality to connect in real time and fix the impending problem swiftly, meaning little or no interruption to production. Everything is in place, even with last minute changes– your new car is ready to roll!
Innovations in Industry 4.0 mean better quality services and products, more efficient use of materials and improved safety standards. These innovations are not the stuff of science fiction; they are a reality of modern manufacturing today, regardless of scale and size.
Related: IBM's Juan Jose De La Torre On The Need For MENA Businesses To Embrace Digital Transformation